
Tutkimus, kehitys ja palvelut
Tarjoamme tietomme ja taitomme työelämän käyttöön, sillä yhteistyöllä ja uutta oppimalla saamme aikaan oikeasti tärkeitä asioita tulevaisuutta varten.
Tutkimme ja kehitämme kanssasi
Panostamme vahvaan tutkimus, kehitys ja innovaatio-osaamiseen, joka jakautuu kuuteen eri tiimiin: digitalisaatio, tuotantotalous, yrittäjyys ja liiketoiminta, hyvinvointi ja terveys, kemia ja biotalous, sekä hankevalmistelu ja verkostot.

Hankkeet
Meillä on jatkuvasti noin sata käynnissä olevaa hanketta, joissa etsimme ja kehitämme ratkaisuja paikallisesti, valtakunnallisesti ja kansainvälisesti. Tutustu hankkeisiimme!

Kehittämis- ja koulutuspalvelut
Meiltä saat tukea yrityksesi toiminnan ja osaamisen kehittämiseen. Hyödynnämme palveluissamme asiantuntijajoukkomme osaamista ja laboratorioidemme laitteistoja.

Kehitysympäristöt
Alueen yritysten kehittyminen ja osaavan työvoiman saatavuus varmistetaan ajantasaisilla investoinneilla kehitysympäristöihin ja niiden ympärille rakentuvilla tutkimushankkeilla.
Tutustu kehitysympäristöihimmeOpiskelijayhteistyö
Työharjoitteluilla, opiskelijaprojekteilla ja opinnäytetöillä opiskelijamme saavat tuntumaa työelämään. Samalla yritykset ja yhteisöt saavat kosketusta tuleviin osaajiin.
OpiskelijayhteistyöVuokraa tila
Oletko järjestämässä kokousta tai koulutusta, joihin yrityksesi omat tilat eivät tahdo taipua? Pietarsaaren kampuksellamme on monia erikokoisia luokka- ja kokoustiloja, joita on mahdollista vuokrata.
TilavuokrausJulkaisut
Julkaisusarjoissamme esitellään muun muassa projekteissa työskentelevien henkilöiden osaamista, ajankohtaisia hankkeita ja tasokkaita opinnäytetöitä.
Tutustu julkaisuihimme
Talent Boost
Työnantaja, etsitkö kansainvälistä osaajaa yritykseesi tai toimintaasi? Centrian Talent Boost –toiminta keskittyy erityisesti Centria-ammattikorkeakoulun toiminta-alueen kansainvälisten osaajien työllistämiseen ja työllistymisen edistämiseen sekä yritysten ja kansainvälisten osaajien parempaan kohtaamiseen.
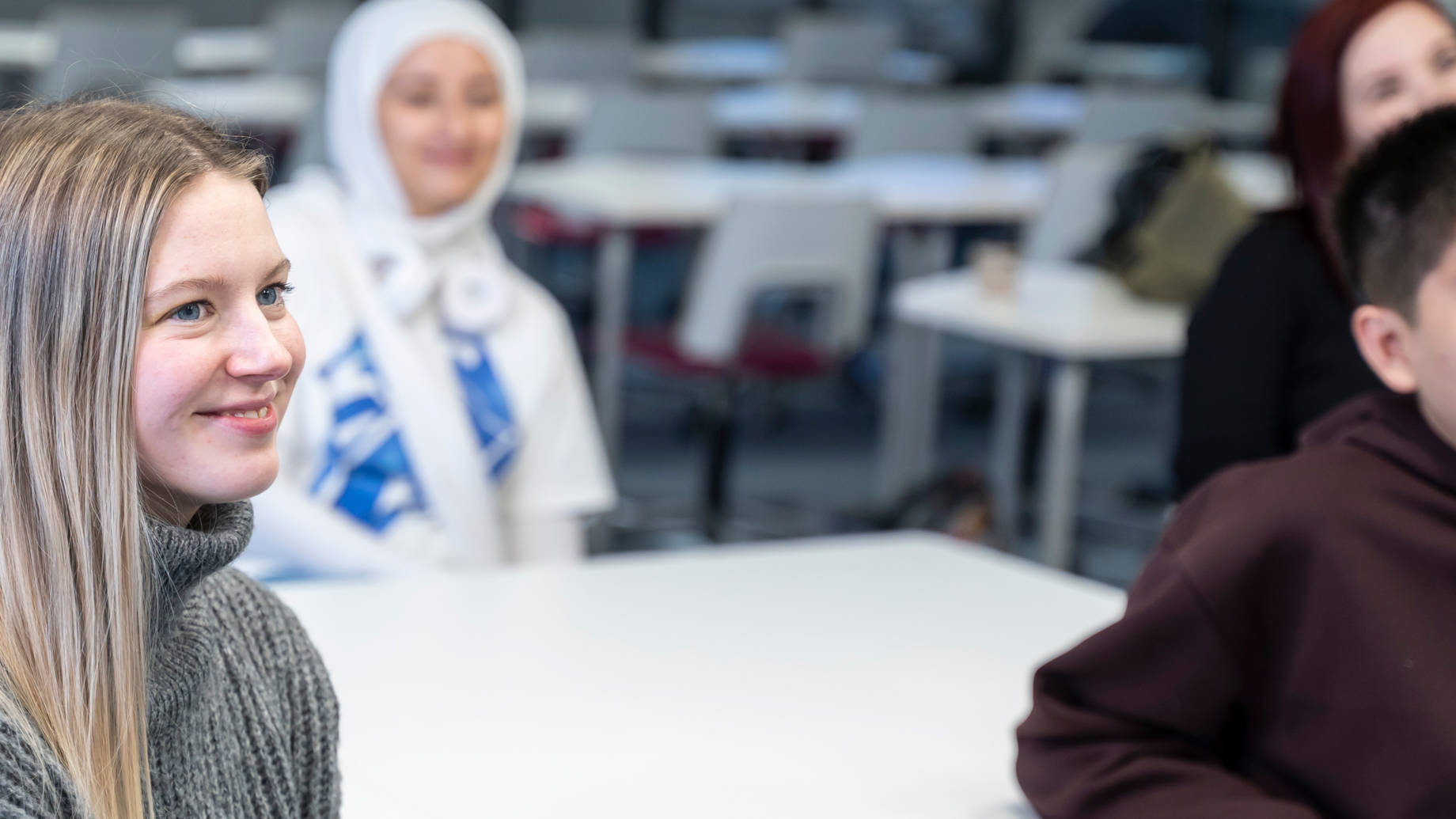
Pedagogiikan kehittäminen
Centria kehittää aktiivisesti korkeakouluopetusta sekä koulutusaloittain että yleisesti pedagogiikan saralla.
AJANKOHTAISTA
Centria koulutuspalvelut järjestää TYHY/TYKY-toimintaa työyhteisöille
Centria koulutuspalvelut järjestää TYHY/TYKY-toimintaa työyhteisöille. Tilaus räätälöidään aina tilaajan toiveiden mukaisesti ja yksilöllisesti. Työpajojen fasilitoijilla on vahva osaaminen vuorovaikutuksesta ja psykologisesti turvallisen ilmapiirin luomisesta. Valitusta …
NLP Master Practitioner -utbildning i Jakobstad 9.8.–24.11.
Vad är det fråga om? I stället för att vänta och hoppas att omgivningen skall ändra på sig, kan vi börja använda modeller till att …
Kokemuksia ilmaiswebinaarien järjestämisestä
Centria koulutuspalvelut toteutti maalis-huhtikuun aikana kolmen ilmaiswebinaarin sarjan M365-koulutusaiheista Excel, PowerPoint sekä Word. − Koulutussarja oli onnistunut kokemus, toteaa koulutuspäällikkö Hannele Häli. Webinaarit kestivät kerrallaan …
AVAINLUKUJA

Ura Centriassa?
Meillä pääset tekemään työstäsi itsesi näköisen ja kehittymään toivomaasi suuntaan. Centrialaisen työarki ei ole vain työssä jaksamista vaan aitoa työssä viihtymistä. Kattava työterveyshuoltomme kantaa tiukoissakin paikoissa, ja harvinaisen runsaat liikunta- ja kulttuurietumme tuovat arkeen uutta potkua. Meille myönnetty Great place to work -tunnus on merkki siitä, että teemme oikeita asioita, joilla on merkitystä.